Models to predict thermo-mechanical loading often need to account for microstructural evolutions in 3D to predict multi-axial loading via the introduction of internal state variables (ISVs) that describe the microstructural states. These ISVs pose, however, a great challenge when it comes to their calibration. Indeed, in situ 3D characterizations are then needed How to achieve that? Focused ion beam (FIB)-scanning electron microscopy (SEM) is a destructive technique and, therefore, cannot be used to follow the microstructure. If the microstructural features are sufficiently different (chemically or crystal orientation), X-ray diffraction under synchrotron radiation could be used. What if that is not the case? To make it possible, 3D phase-field simulations seem a best-suited approach to gain in situ 3D information. Thus, we performed phase-field simulations to be used for the calibration of advanced microstructurally-sensitive models.
What are we trying to achieve?
We strive to develop microstructure-sensitive models and calibrate them using 3D phase-field simulations mimicking complex thermo-mechanical loading such as non-isothermal loading. This allows us to improve the predicting capabilities of the models by being more realistic on the coupling between microstructure-dislocation interactions.
We received several grants to fund this research:
- YIP Air Force : Microstructural Instabilities in Single Crystal Metals for Extreme Environments↗ (PI : J.B. le Graverend ; $358,869 ; April 2017-March 2021)
Abstract
As the US Air Force fleet continues to age, a greater portion of its budget will be required to ensure safe and effective operations beyond the design service life. In fact, for various military vehicles and platforms, the recommended service life for safe operation is projected to increase by a factor of 1.5 to 5 AFRL, 2014. The high demand for safety and cost reduction culminates in the case of materials systems operating under extreme environments such as turbine blades made of Ni-based single crystal superalloys. Turbine blades are used in the hot section of the engine and are, therefore, subjected to multiaxial high-temperature viscoplastic deformations, namely, creep and dwellfatigue, due to both their complex geometry and their advanced design, e.g., internal cooling channels aimed to increase the exhaust-gas temperature during in-service operations.
- NSF : Non-isothermal Viscoplasticity in Metals (PI : J.-B. le Graverend, Co-PI : A. Benzerga ; $488,001 ; May 2020-April 2023)
Abstract
The underlying hypothesis of this project is that the lattice misfit between phases in Nickel-based superalloys under certain non-isothermal loadings plays an essential role in enhancing creep performance at elevated temperatures. The project, therefore, rests on the transformative paradigm that ?hotter can be longer? depending on how the coherency stresses evolve. To test this hypothesis, the lattice misfit evolution will be tracked in new temperature/stress regimes by in situ X-ray diffraction under synchrotron radiation. In situ results will be used to correlate, at the macroscale, the non-isothermal mechanical responses. Furthermore, discrete dislocation dynamics simulations will be carried out to gain further insight into dislocation/precipitate interactions depending on the microstructural state and lattice misfit. These simulations will help identify and quantify competing mechanisms, e.g., climb/glide and self-interaction/precipitate hardening effects, which will qualitatively help explain experimental results.
- ONR : Unraveling High-Temperature Creep-fatigue-oxidation in Metals (PI : J.B. le Graverend ; $445,861 ; June 2020-June 2023)
Where can that be used?
The approach followed could be used on any materials and on any applications to improve the safety and reduce the costs of apparatus used in extrem conditions.
Who is involved?
J.-B. le Graverend (PI)
Amine Benzerga (Co-PI)
H. Rajendran (Alumni)
J. Dominic (Ph.D. Student)
Who is funding?
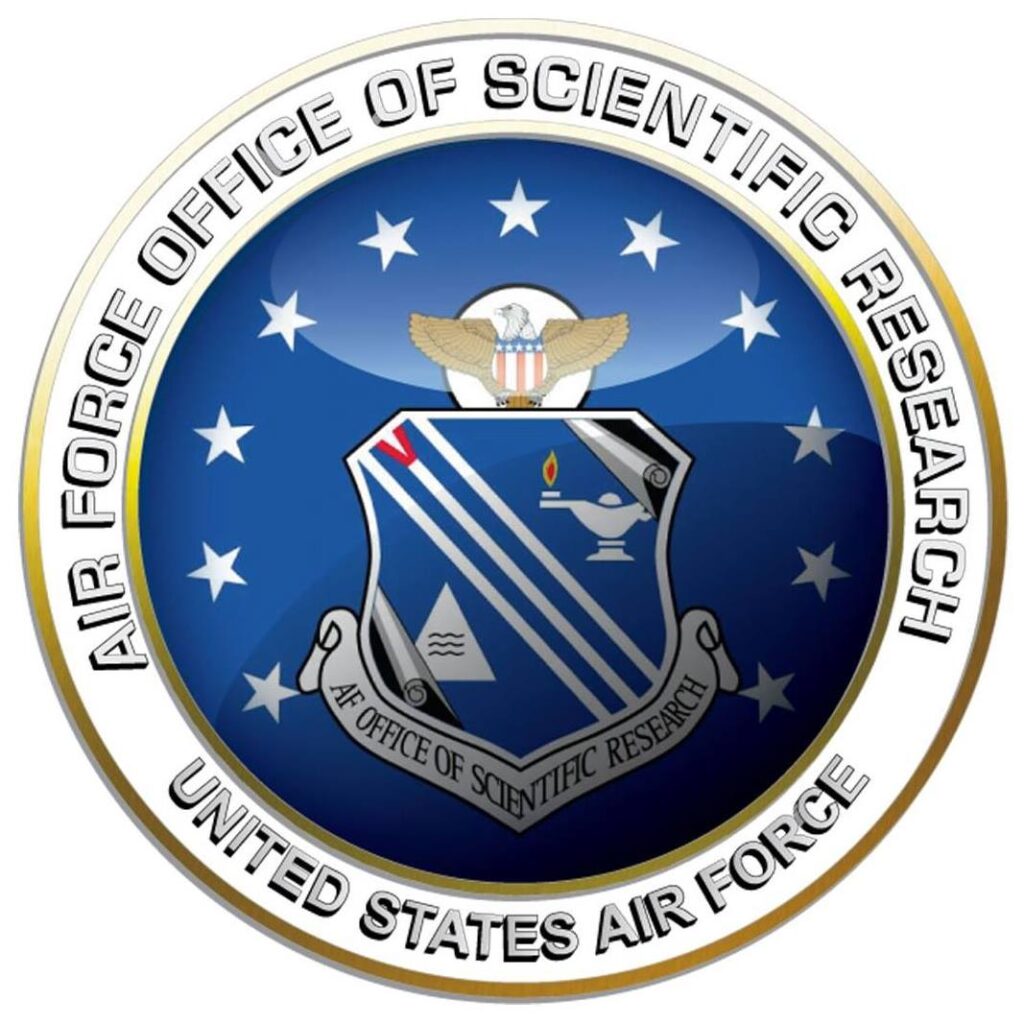
Air Force Office of Scientific Research
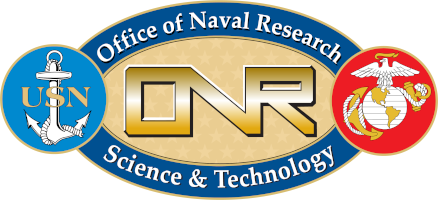
Office of Naval Research
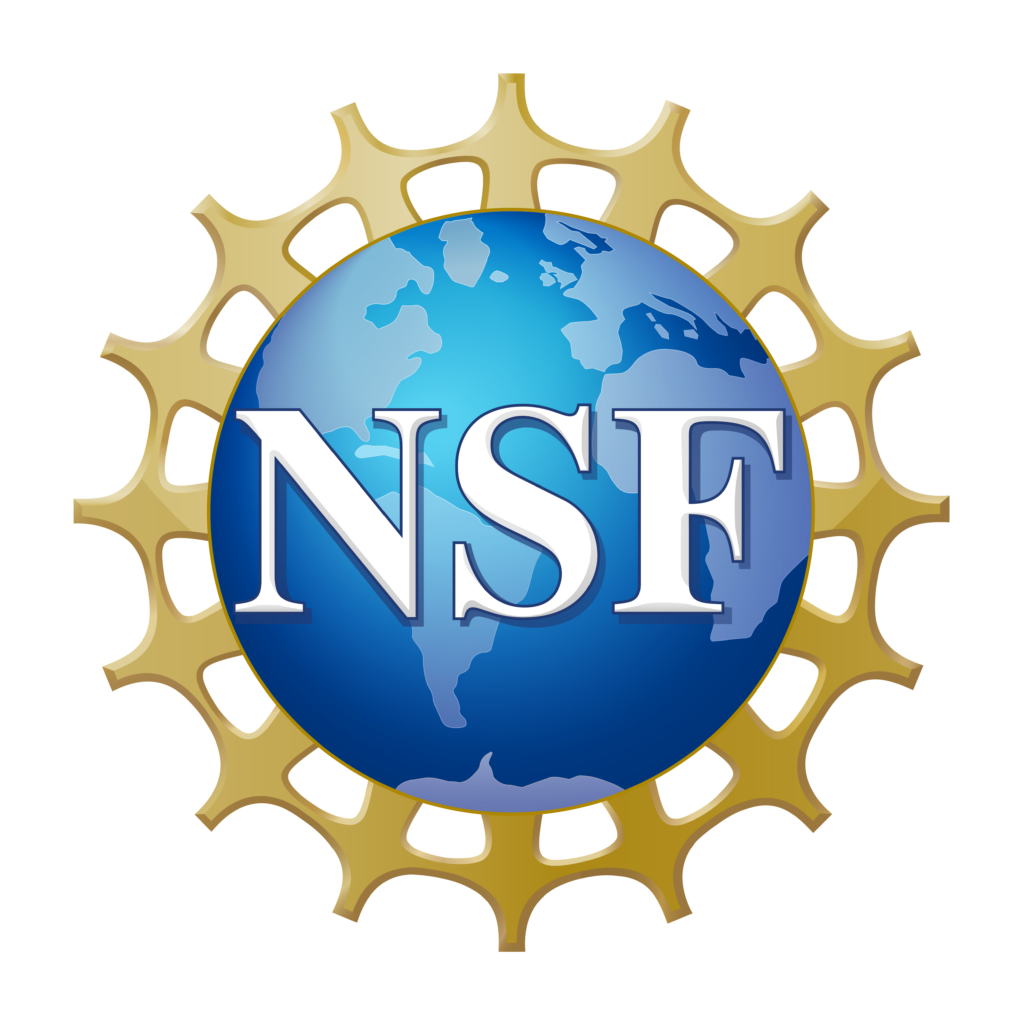
National Science Fondation
Publications and Conferences
Published papers :
- A Lattice-misfit-dependent Micromechanical Approach in Ni-base Single Crystal Superalloys
J.-B. le Graverend* & R. Harikhrishnan
Journal↗, Date - Finite-Element Crystal Plasticity on Phase-Field Microstructures: Predicting Mechanical Response Variations in Ni-Based Single-Crystal Superalloys
J.-B. le Graverend* & R. Harikhrishnan
Journal↗, Date - A creep-damage phase-field model: Predicting topological inversion in Ni-based single crystal superalloys
R. Harikhrishnan & J.-B. le Graverend*
Journal↗, Date
Conferences :
- TMS 2020, San Diego (CA), USA, February 23-27, 2020
Phase-field-informed Modeling of γ’ Rafting in 3D during
High-Temperature Creep in Ni-based Single Crystal Superalloys
J.-B. le Graverend & R. Harikrishnan - Euromat 2019, Stockholm, Sweden, September 1-5, 2019
Phase-Field-Informed Modeling of γ’ Rafting in 3D during High-Temperature Creep in Ni-Based Single Crystal Superalloys
J.-B. le Graverend & R. Harikrishnan - Euromat 2019, Stockholm, Sweden, September 1-5, 2019
Finite-Element Crystal Plasticity on Phase-Field Microstructures: Predicting Mechanical Response Variations in Ni-based Single-Crystal Superalloys
J.-B. le Graverend & R. Harikrishnan - TMS 2019, San Antonio (TX), USA, March 10-14, 2019
Finite-Element Crystal Plasticity on Phase-Field
Microstructures: Predicting Mechanical Response Variations in Ni-based Single-Crystal Superalloys
J.-B. le Graverend & R. Harikrishnan - ICTAM 2016, Montreal (QC), CA, August 21-26, 2016
3D Modeling of γ’-Rafting for Predicting Viscoplastic Deformations in Ni-Based Single Crystal Superalloys
J.-B. le Graverend (Sp)