Damage is defined as a discontinuity of matter, such as voids, in the Continuum Damage Mechanics Theory. However, microstructural changes also lead to mechanical degradations and should, therefore, be better investigated to gain new insights into mechanical performances. It is especially true at high temperatures where microstructural evolutions are facilitated due to increased diffusion coefficients. This is why Ostwald ripening (aka isotropic coarsening) or directional coarsening may occur and change the mechanical response during, e.g., creep and fatigue. New predictive capabilities are implemented in the phase-field and crystal-plasticity framework.
What are we trying to achieve?
Microstructural evolutions, plasticity, and damage are closely intertwined. This is especially true at high temperatures since microstructural changes could quickly lead to permanent/transient hardening/softening phenomena. Continuum damage mechanics predict that hotter is shorter, while the PI has experimental evidence that this is not always the case. This paradigm shift should be accompanied by the formulation of new damage density functions for improved predictive capabilities as well as new ways to predict degradated microstructures.
Here is the grant we obtained to work on this topic:
- YIP Air Force : Microstructural Instabilities in Single Crystal Metals for Extreme Environments↗ (PI : J.B. le Graverend ; $358,869 ; April 2017-March 2021)
Abstract
As the US Air Force fleet continues to age, a greater portion of its budget will be required to ensure safe and effective operations beyond the design service life. In fact, for various military vehicles and platforms, the recommended service life for safe operation is projected to increase by a factor of 1.5 to 5 AFRL, 2014. The high demand for safety and cost reduction culminates in the case of materials systems operating under extreme environments such as turbine blades made of Ni-based single crystal superalloys. Turbine blades are used in the hot section of the engine and are, therefore, subjected to multiaxial high-temperature viscoplastic deformations, namely, creep and dwellfatigue, due to both their complex geometry and their advanced design, e.g., internal cooling channels aimed to increase the exhaust-gas temperature during in-service operations.
Where can that be used?
Extreme conditions often come with fast changes. One example could be found in the certification procedure of helicopter engines that requires testing engines against One Engine Inoperative (OEI) conditions that lead to temperature increases from 1050C to 1200C in 3/4 seconds and hold it for 30 seconds. These thermal jumps lead to a massive dissolution of the strengthening phase and the formation of small precipitates, which interact with dislocations, when the temperature returns to 1050C. Better understanding microstructural evolutions is key to improved modeling and, therefore, lifetime predictions.
Who is involved?
J.-B. le Graverend (PI)
H. Rajendran (Alumni)
S. Lee (Alumni)
Who is funding?
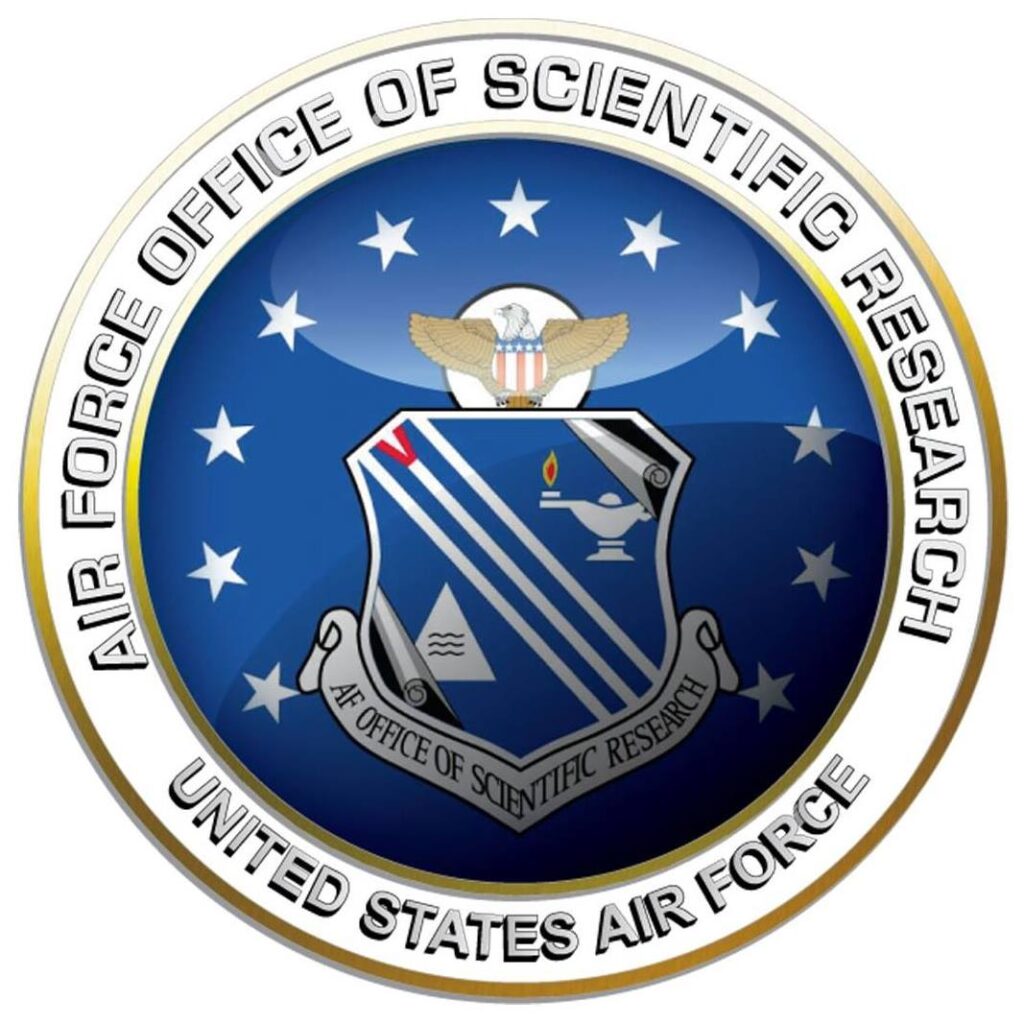
Air Force Office of Scientific Research
Publications and Conferences
Published papers :
- A Lattice-misfit-dependent Micromechanical Approach in Ni-base Single Crystal Superalloys
J.-B. le Graverend* & R. Harikhrishnan
International Journal of Mechanical Sciences↗, April 2021 - Finite-Element Crystal Plasticity on Phase-Field Microstructures: Predicting Mechanical Response Variations in Ni-Based Single-Crystal Superalloys
J.-B. le Graverend* & R. Harikhrishnan
Journal of Material ↗, June 2019 - A creep-damage phase-field model: Predicting topological inversion in Ni-based single crystal superalloys
R. Harikhrishnan & J.-B. le Graverend*
Materials & Design↗, December 2018
Conferences :
- TMS 2020, San Diego (CA), USA, February 23-27, 2020
Phase-field-informed Modeling of γ’ Rafting in 3D during
High-Temperature Creep in Ni-based Single Crystal Superalloys
J.-B. le Graverend & R. Harikrishnan - Euromat 2019, Stockholm, Sweden, September 1-5, 2019
Phase-Field-Informed Modeling of γ’ Rafting in 3D during High-Temperature Creep in Ni-Based Single Crystal Superalloys
J.-B. le Graverend & R. Harikrishnan - Euromat 2019, Stockholm, Sweden, September 1-5, 2019
Finite-Element Crystal Plasticity on Phase-Field Microstructures: Predicting Mechanical Response Variations in Ni-based Single-Crystal Superalloys
J.-B. le Graverend & R. Harikrishnan - TMS 2019, San Antonio (TX), USA, March 10-14, 2019
Finite-Element Crystal Plasticity on Phase-Field Microstructures: Predicting Mechanical Response Variations in Ni-based Single-Crystal Superalloys
J.-B. le Graverend & R. Harikrishnan - ICTAM 2016, Montreal (QC), CA, August 21-26, 2016
3D Modeling of γ’-Rafting for Predicting Viscoplastic Deformations in Ni-Based Single Crystal Superalloys
J.-B. le Graverend